So, this is going to be a ridiculous update. I am hoping to finish this project by the end of this week. What you are going to see is something really different to the Honda (car) guys are used to seeing. The motorcycle guys are used to seeing megaphones and whatnot, but maybe not some of the other stuff that I'm incorporating into these headers.
Stack of awesome bends, transitions and cones from Columbia River Mandrel Bending:
If you EVER need bends, then buy them from CRMB. They are exactly consistent, well priced and have EXCELLENT customer service.
Here's my cheap but actually trusty band saw:

I like it. It's not as nice as the Milwaukee I would prefer to have, but . . . At $65 shipped, this gets the job done incredibly well.
Capturing the scale of these parts is difficult without a frame of reference.
The first order of business was to flap-wheel the bead left from the weld on the cones, which looks something like this:

Here I am getting the reverse (convergent) cone marked for cutting:

Here it is marked up and ready to get chopped:

Here is the setup I came up with for clamping, which worked very well:
Fit-up is pretty effing good:
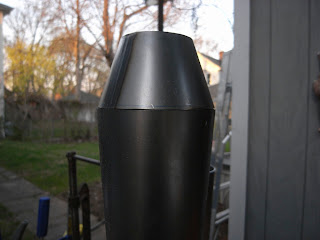
That's all I needed to do for the larger megaphone. The smaller one, which is more "normal" sized needed some trimming to fit, so, here are some pics of that:
And here's a pic of the megaphone set up to see how it will look with the 2.5" tube that will get a V-band to fit the rest of the rest of the exhaust:
Now, for some perspective and scale:

Yeah . . . the large one is insane. I wanted to go )(#*$(*#$ huge to see WTF happens. I don't think anyone has ever used one this large on a Civic or CRX. I want to see what happens. Megaphones are proven to work, so, I figure go to the extreme with one and see what happens. If it doesn't work, I can easily cut it down in increments. =)
"Bench" cleanup time:
Now we get into some of the more creative. Taking the 18* bends and making a 2-1 collector that is both precise and consistent isn't terribly easy without a shop full the proper tools, so . . . I made molds. I spaced the bends using wood spacers and using clear tape over the end of the tubes.
Here are the molds for the two sizes of tubing I am using:
Here's the taped end I used to make the mold:
I simply used packing tape over the end of the tube, cement in a chinese food container and time. Once the mold was dry, I just plopped the other bends into the mold, sprayed them with cheap spray paint, thanks to my friend Jesse's brilliant idea, then cut them.
I didn't get a lot of pics of the in between stages. I got all the beds cut up, got a TIG welder, got that set up in a friend's garage (I don't have 220V access at home) and got to welding.
Here are most of the collectors welded up:
Some closeups of the welds on the collectors:

Inside:
Not pretty, but, honestly, not bad for my first TIG work on thin metal. It cleaned up nicely enough with a die grinder. Also, not the exact fitment in the "crotch."


Keep in mind, these are the first TIG welds I laid down in YEARS. Every time I sit down to it, I get better, more comes back, I get into the rhythm faster. I'm near ready to tackle some stainless. I'm looking forward to it.
The next step was to take the collectors and match them up to the size they need to be, thusly:
A crack developed when sizing the ends:

I'm not worried about it because I have a TIG welder. heh
I also managed to break my cheap exhaust expander trying to expand stuff.
I was seriously pissed. There don't seem to be and good solutions for this, either. I bought a heavier duty expander, but . . . it won't fit in the smaller tubes. I'm using 1 5/8" OD.
This is the fit I am looking for:


Keep in mind . . . this is JUST the collector. heh heh heh
Unt Hello! Here's the collectors 90% finished:
HUUUUUUGE!
OH YEAH!
Awesome! I love that megaphone.
ReplyDeleteHoly moley!
ReplyDelete=)
ReplyDeleteNice work! What size does the big one expand out to?
ReplyDelete4" IIRC. I'll measure it again. I need to get all my measurements down now that I am mocking up the primaries on Chris' header.
ReplyDelete